Identify your data gaps and start to retrofit now
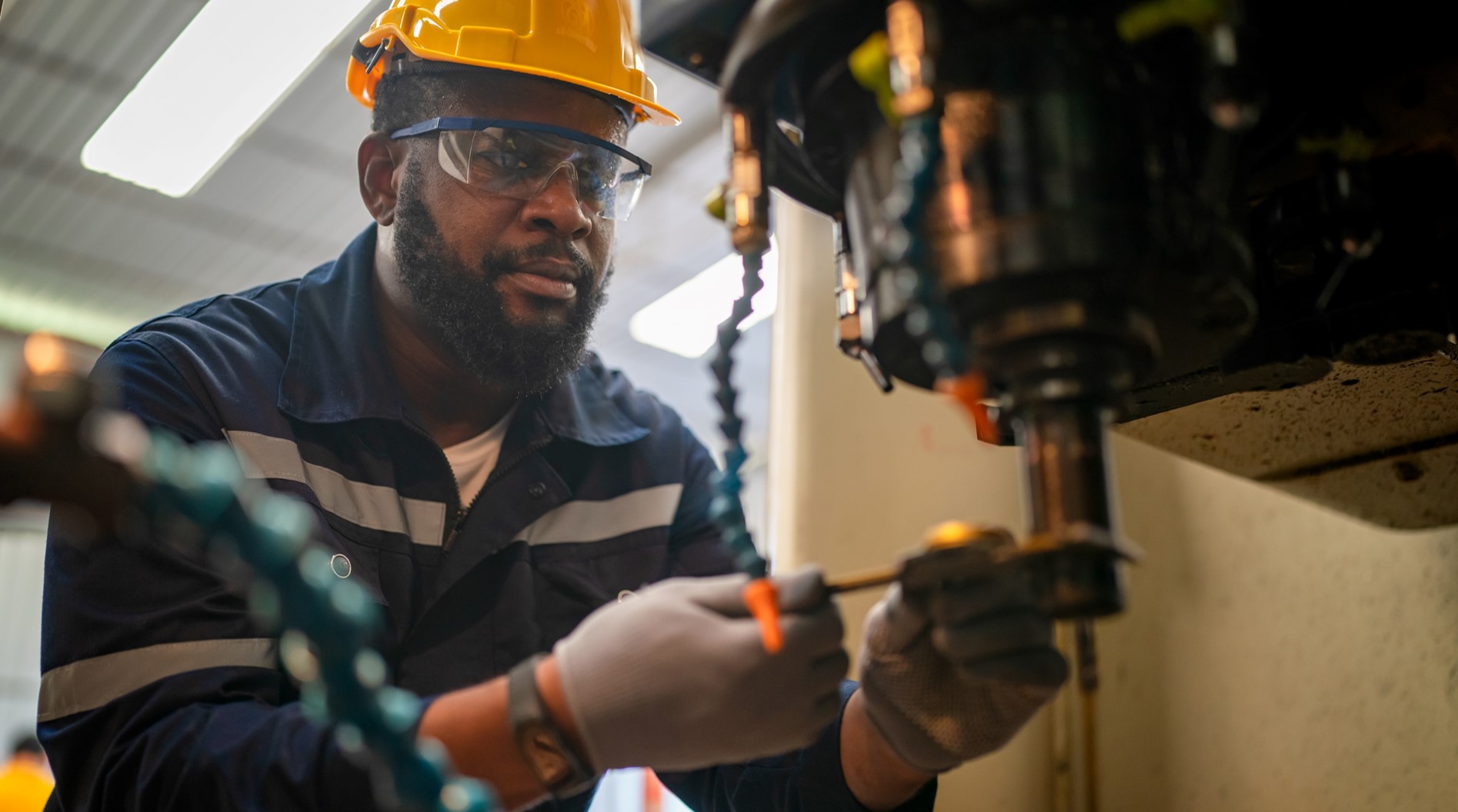
Take advantage of Industry 4.0 by retrofitting your machines for data acquisition
In the insight Streamlining Data Acquisition Process, we talked about the challenges of getting data and how to overcome it.
To summarize, getting the right data, in the right format, and in the right quality is not an easy task. And therefore, we suggest starting with a value-driven approach. And that’s what we call Data Gap Analysis.
Once the hurdle of ‘what?’ is crossed, the next one of ‘how?’ comes up. Retrofitting machines for gathering machine data is a common approach. From our client experiences, we know that this requires step-by-step planning. Let us help to reduce your efforts by giving you a piece of advice on - How to Retrofit?
1. First step
The first step is to assess what is already existing.
Check if the required data is already in the existing IT and control systems (e.g., ERP, MES, IoTPlatform, etc.) and evaluate if the data has the necessary specifications and quality.
- It is uncommon for all relevant data to be available or of appropriate quality. In older IT systems, a lack of interfaces might make it difficult to retrieve the data.
- For a predictive maintenance use case, vibration and motor current are required. In reality, these parameters are often not recorded. If they are, it must be validated that the data is measured at the proper frequency.
2. Second step
If the data is not already available in existing data sources or if it is not use-case worthy, then move to the next point.
Verify whether the data is already being tracked by the PLCs and machine control. In many cases, data from the sensors used for machine control might be useful. This can be done by retrofitting sniffing devices to tap PLC and sensor data.
- Be aware that accessing PLC/control systems may void warranty claims. Therefore, the impacts on the control systems need to be taken into account. For example, accessing high-frequency data across an automation network may result in bandwidth restrictions and control system impairment.
- Predictive maintenance on CNC machines requires high-frequency vibration and current data. This can quickly congest the automation network. However, the control network is also in charge of performing high-precision operations, necessitating real-time communication between sensors, controllers, and actuators.
3. Third step
If accessing the data from the current sensor infrastructure does not seem like a feasible option, here’s what you can do next.
Check if sensors can be retrofitted to measure the desired value.
- Along with the measurement technology itself, take into account how it will be integrated with IT and IoT systems. Smart IoT sensors can be a simple solution to integrate.
4. Fourth step
Don’t give up if the direct measurement of the parameter is too complex, it still might be possible to implement the use case.
In some circumstances, it might not be technically or financially feasible to obtain the desired values. Direct measurements are simply not possible due to the limited access area, extreme climatic conditions, such as high temperatures, etc.
- Evaluate the measurement possibilities and whether the required measurement may be derived from that value. For example, measuring the amount of CO2 generated from organisms can be used to determine the reaction status of a biochemical reaction.
- In the case of milling, very accurate assumptions can be made about the surface quality from vibration data using machine learning.
A last important step for data acquisition is to plan the integration into the existing and future IoT-Architecture and ensure that the developed I4.0 application can be efficiently scaled up, e.g., through the use of consistent data models.
Let's connect!
Found this insightful? Also read our other posts in this series related to machine data acquisition or contact us directly!
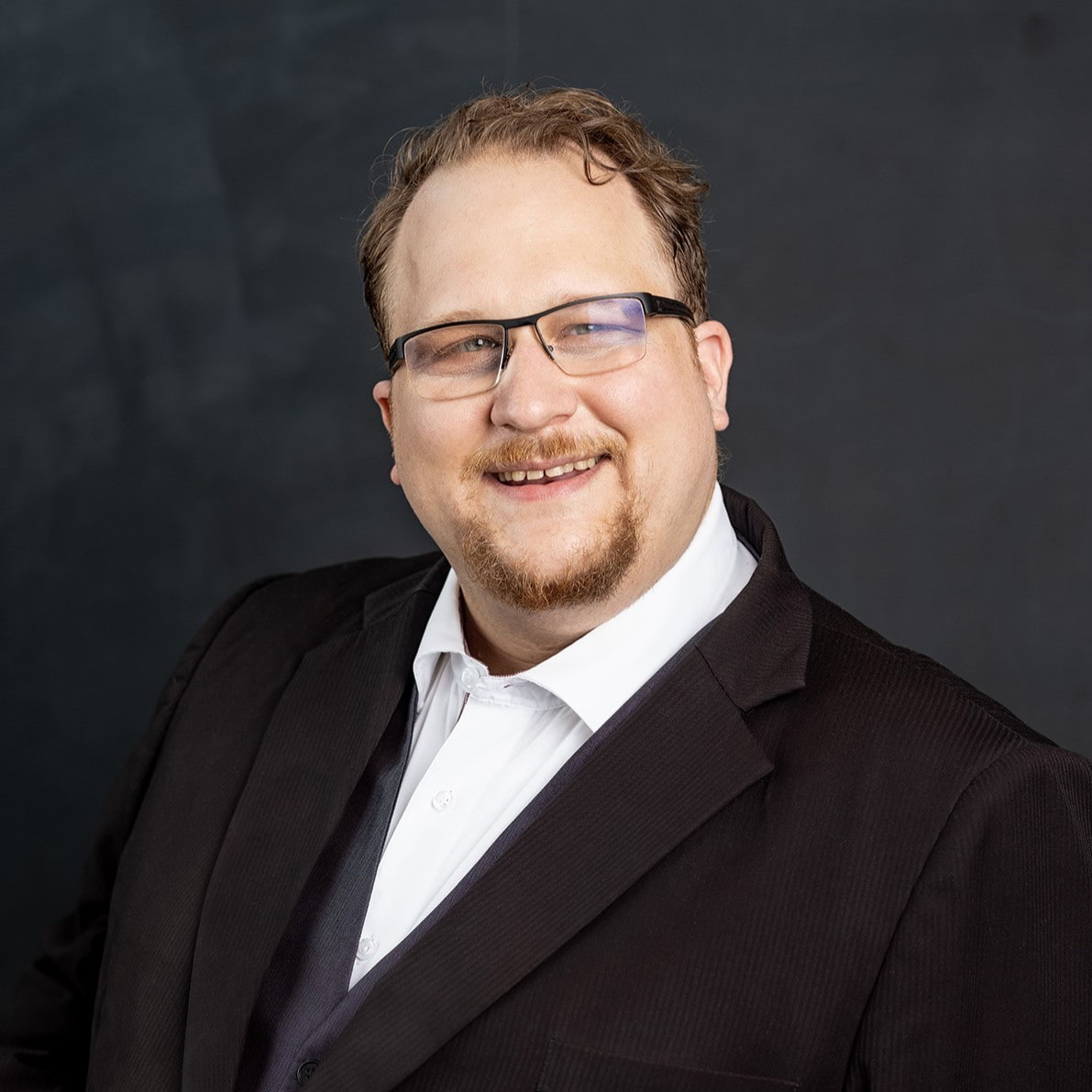
Subscribe to receive the latest insights directly to your inbox.